Single-chainring (1X) drivetrains are de rigueur for mountain and cyclocross bikes, and it’s easy to see why. These drivetrains require fewer overall parts, which decreases cost, weight, and even aerodynamic drag. The single shift lever also simplifies gear shifts.
But do these innovative drivetrains produce more or less friction than traditional ones? We set out to discover the answer. One might assume that a 1x system is more efficient due to the fewer number of parts. There are other dynamics at play, however, in this equation. The more a chain moves laterally, the more friction it produces, potentially giving the upper hand to a traditional 2X system.
For our test we used the labs at CeramicSpeed USA in Boulder, Colorado. CeramicSpeed’s chief technology officer Jason Smith conducted the tests; Smith founded FrictionFacts, a friction-testing laboratory acquired by CeramicSpeed in 2014. Smith has developed precision equipment for testing drivetrain efficiency, and uses it to measure how many watts of a rider’s power are lost within a bicycle’s moving parts.
Let’s take a closer look at our test methods and the final results.
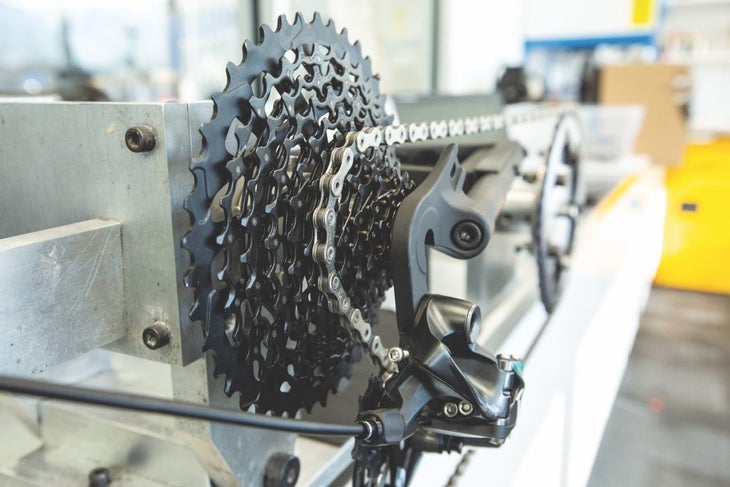
Test protocol
The 1X setup comprised a SRAM Force 1 rear derailleur, 48-tooth X-Sync narrow-wide-tooth (NW) chainring, PC-1170 chain, and 10-42-tooth cassette. The 2X drivetrain included a Shimano Ultegra rear derailleur, 39-/53-tooth chainrings, CN-HG701 chain, and 11-34-tooth cassette. We simulated a rider output of 250 watts pedaling at a cadence of 95RPM with both setups, and used the same total gear range.
We ran both chains on the test machine for the same time, then stripped away the factory lubricant, and re-lubed them with additive-free mineral oil. We selected cogs to create the approximate same gear ranges for both setups.
We measured the chain-line on each setup as well as the amount of lateral offset in every non-aligned gear combination. The 1X chainring was aligned with the fifth from smallest cog. The 53-tooth chainring of the 2X drivetrain was also aligned with the fifth from smallest cog, while the 39-tooth chainring of the 2X was aligned with the eighth from smallest cog.
Results
The 2X drivetrain had lower frictional losses in every gear than the 1X system—with the caveat that the chainrings matched up with the ideal cogs in the rear. The average friction within the 1X drivetrain was 12.24 watts. This was computed as the sum of the drivetrain power losses in each of the 11 gears divided by 11. The average friction of the 2X drivetrain was 9.45 watts, computed as the sum of the power losses in each of the 15 optimal gears divided by 15. This is just under a three-watt average difference between the two drivetrains.
The frictional losses of the system were highest for each chainring when the chain ran on the smallest cog. This is also where the difference in frictional losses were greatest between the two drivetrains: at the highest gear ratio (4.8) the 48 X 10-tooth combination consumed six watts more than the 53 X 11-tooth combination.
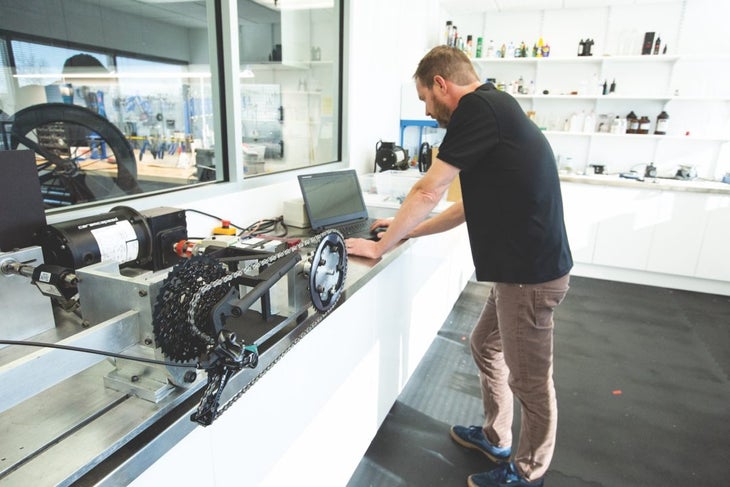
Why the variation?
The chain creates the most friction. The jockey-wheel (pulley) bearings create a small amount. Smith’s previous research also indicates that the clutch in the SRAM 1X rear derailleur adds no friction.
Chain friction will increase due to increased lateral angle, increased chain tension, and increased link articulation (folding).
Cross-chaining robs power due to the plates scraping harder on each other. Smith’s prior research reveals how cross-chaining and chain articulation angles and rate affect friction.
Higher chain tension increases drag by pulling harder on the pivot pins and by forcing the rollers harder against the teeth of the chainring and cog.
Chain articulation is essentially how many degrees the chain hinges at each pin to get around a chainring, cog, or pulley wheel, and how many times per second the chain goes through those articulations; power loss increases with increases in either one. Articulation rate increases with increasing chain speed. The larger the chainring at a given cadence, the higher the chain speed and the higher the articulation rate, and consequent frictional energy losses.
Previous FrictionFacts testing shows that narrow-wide teeth create no more friction when cross-chaining than do standard, uniform-thickness (i.e., 2X or 3X) chainring teeth, since every tooth on a narrow/wide-tooth chainring pulls the chain over the same amount; it moves narrow and wide chain links laterally the same distance. With a standard chainring working at the same cross-chain angle, the teeth don’t pull over the wide chain links, but every other tooth pulls the narrow chain links over twice as far as each tooth on an NW pulls a chain. It’s a wash, friction-wise.
However, even when the chain is perfectly aligned in the 48 X 18-tooth, 53 X 19-tooth, and 39 X 25-tooth gears—hence no frictional losses due to cross-chaining—the 1X system consumes more power than the 2X on either chainring. Why is that?
The major reason is higher articulation angles of the chain due to the chain going over a smaller cog on the 1X; this forces the chain to bend more around the cog.
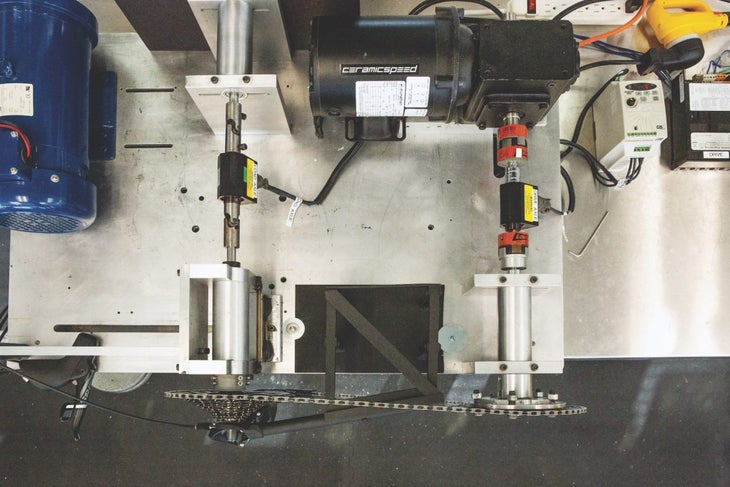
Tension on the upper span of a chain is inversely proportional to chainring size: The smaller the chainring, the higher the chain tension. That comes down to simple physics. Power output can be simplified to RPM x Torque. Torque is transferred from the chainring to the cogs by means of the chain tension. Since power output and cadence are constant in this test, RPM and Torque are identical in both larger and smaller chainrings. Thus, the chain tension (force) on a smaller chainring must be higher, as Torque is given by the equation Torque = Force X Radius, and the radius is smaller. Conversely, a larger chainring has a larger radius, and therefore the chain tension—and hence consequent friction—must be lower at the same RPM and power output.
This brings us to the relationship between frictional losses due to articulation and those due to gear ratios. Previous CeramicSpeed/FrictionFacts 2X drivetrain tests indicate there is a frictional minimum when the cog is aligned with the chainring. With the larger, 11-34-tooth and 10-42-tooth rear cassettes of this test, the friction continues to drop at a lower rate (lower slope to the graph) as the cog size continues to increase. With the smaller chainrings, the reduction in drag due to the reduced angular articulation around the large cogs exceeds the increase in drag due to cross-chaining.
The takeaway
Congrats, 2X drivetrain users. With the gear ratios used in our test, a 2X drivetrain is typically more efficient than a 1X drivetrain. Of course, this efficiency can be impacted by a wide range of variables. Aftermarket oversized pulley wheels reduce chain-link articulation angles, thus improving efficiency. Higher rear derailleur spring tension increases friction. Chain efficiency and even chain lube also impact friction. For instance, past FrictionFacts tests showed Shimano chains to have lower friction than SRAM chains; if that difference still exists, one could reduce the difference in efficiency by using the same chain on both drivetrains.
The above graph illustrates a few things: Should a rider use the inner chainring on a 2X with any of the three smallest cogs, friction will be higher than it is when using the 1X. To achieve 2X efficiency gains, a rider must only use the inner chainring with the largest seven cogs. By contrast, the outer chainring of the 2X is more efficient on any cog than the 1X is in any cog. For riders seeking optimal efficiency, shift from the outer to the inner ring when shifting into the ninth-from-smallest (second-from-largest) cog.
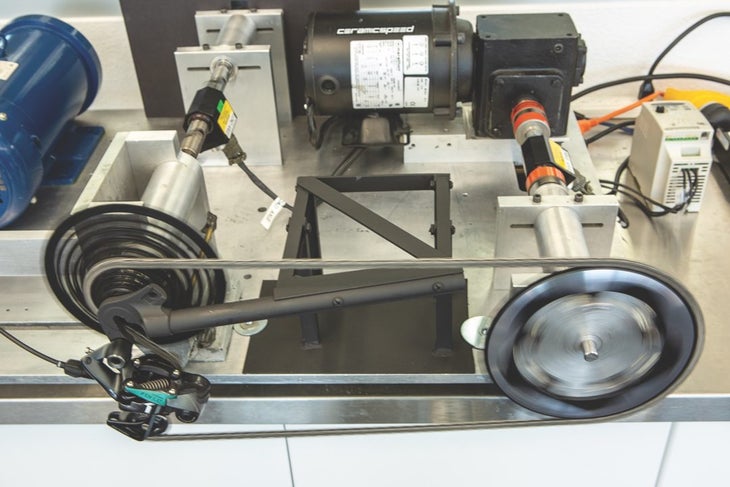
A 1X drivetrain gains aerodynamic performance by eliminating the front derailleur, a front chainring, and a shifter. Some wind tunnel testing performed at 30mph suggests that these savings are about three watts. However, in the higher gears required to pedal sustainably at 30mph, the frictional losses of the 1X are also greater. The aero benefits might be three watts, but they might cost six watts in friction, so the 2X still would win that efficiency battle.
The 1X offers ease-of-use benefits. On the other hand, Synchro Shift on a Shimano Di2 electronic 2X system can be programmed to only select gears that minimize drivetrain friction; the user experience of simply asking a single shifter for an easier or harder gear would be the same as with 1X.
Increasing the chainring size and thus eliminating the 10-tooth cog, and increasing the diameters of all of the cogs, will increase the 1X drivetrain’s efficiency. The tradeoffs, however, include higher weight and possibly higher chainring flex.
A note on the new SRAM eTap AXS
SRAM’s new eTap AXS drivetrain launched after our test. We sent the eTap AXS (12-speed) gear ranges to Smith to examine them, however we were unable to test it against our 1X and 2X setups. The eTap AXS drivetrain features a redesigned rear derailleur with a specially designed clutch mechanism that could, in theory, reduce some friction by lowering chain tension when the mechanism isn’t activated. And the eTap AXS system can be run as a 1X system or a 2X system, so friction numbers depend largely on the setup.
Smith said the AXS’s 10-tooth cog would likely increase friction in the drivetrain, as would the smaller chainrings. SRAM’s new narrow Flattop chain could also impact losses due to friction. However, we simply do not know what the final friction losses are—we will have to wait for our next trip into the lab.